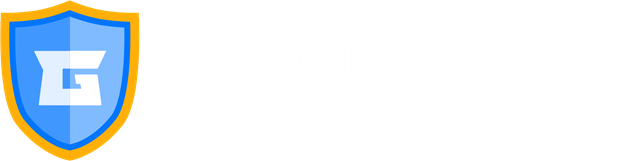
Who Does What – How We Check All the Boxes
The Matrix
Communication and coordination between trades/groups form the backbone of a successful pharmacy project. If these are strong, then the project will likely stay true to the design, under budget, and on-time. Over the years, we have seen how a lack of communication and coordination can bring a project to a screeching halt.
In an effort to reduce last-minute disputes about responsibilities, Guardian Medical teamed up with a Project Leader, Pharmacy Director, and our fellow national associates to create a checklist that assigned duties and responsibilities to the different participating groups.
These groups included:
- Owner/Hospital
- Architect
- MEP Engineers
- General Contractor (and their trades: electricians, carpenters, HVAC, etc.)
- Pharmacy Consultant
- Pharmacy Staff
- Facilities Director
- Security Director
- Owner Network/IT Staff
- Risk Management/Nursing
With some projects taking months to complete, a “Matrix” of duties and responsibilities was invaluable in keeping the project running smoothly. As a shared file, accessible to everyone involved, it served as a reference point confirming responsibility for all aspects of the project.
The Matrix we created identifies over 150 tasks as well as their assigned groups. Though fluid at the beginning of the project, it becomes locked in prior to the start of construction. As with any document assigning responsibility, it is imperative for all groups to collectively review and sign off on each line item. This will then be given to the project leader to hold and refer to during the project, as well as added to the architect’s submittal drawings.
A Few Examples of Matrix Assignments:
HEPA Fan Filter Units
As mentioned in our recent blog, the installation of HEPA Fan Filter Units can become complicated without proper communication and coordination. In many cases, the Pharmacy Consultant provides these units while the General Contractor is tasked with installation, and the Network/IT group connects the units to the Building Automation System (BAS) network.
Cleanroom Doors
The automatic doors in a cleanroom are especially complicated. Not only do you have the company installing the doors themselves, but you also have various electricians running power lines and low-voltage wiring for the handwaves and interlock system. Depending on the size of the equipment to be installed in the room, the doors may also need to be installed at a later date.
Biosafety Hoods
Coordination for the hoods involves the Architect, MEP Engineers, and Pharmacy Staff. Consideration should be given to providing an adequate number of well-placed outlets and locating the hoods to allow for easy cleaning and proper visibility for observation. The correct duct size and its location must be worked out with the MEP Engineers while the correct connection piece must be specified and created with the HVAC installers. Finally, the airflow alarm must be installed.
These are three examples of the many complicated items that go into a pharmacy/cleanroom project. Developing and implementing a matrix of responsibilities is an excellent way to ensure a smooth installation.